棚卸業務の大きな負担
- 膨大な作業時間
- 店舗での棚卸: 平均12時間(営業時間外での作業)
- 倉庫での棚卸: 平均2日間(専任スタッフ複数名が対応)
- 四半期ごとに全拠点で発生する大きな業務負荷
- 人的リソースの圧迫
- 店舗スタッフの残業時間増加
- 倉庫スタッフの本来業務(入出荷)の遅延
- 経理部門での集計・確認作業の集中
在庫精度の問題
- 理論在庫と実在庫の乖離
- 一部店舗では10%以上の誤差が発生
- 倉庫においても数千点規模での不一致
- 手作業による数え間違い
- 深夜・長時間作業によるミスの発生
- 商品の見落としや重複カウント
- 原因特定の困難さ
- 紛失、盗難、誤出荷、計上ミスなど原因の切り分けが困難
- 問題の根本解決が進まない悪循環
システム面の課題
- 既存在庫管理システムの限界
- 入出荷データに基づく理論在庫管理のみ
- 実在庫の効率的な確認手段がない
- 手書き棚卸シートとExcelによる非効率な管理
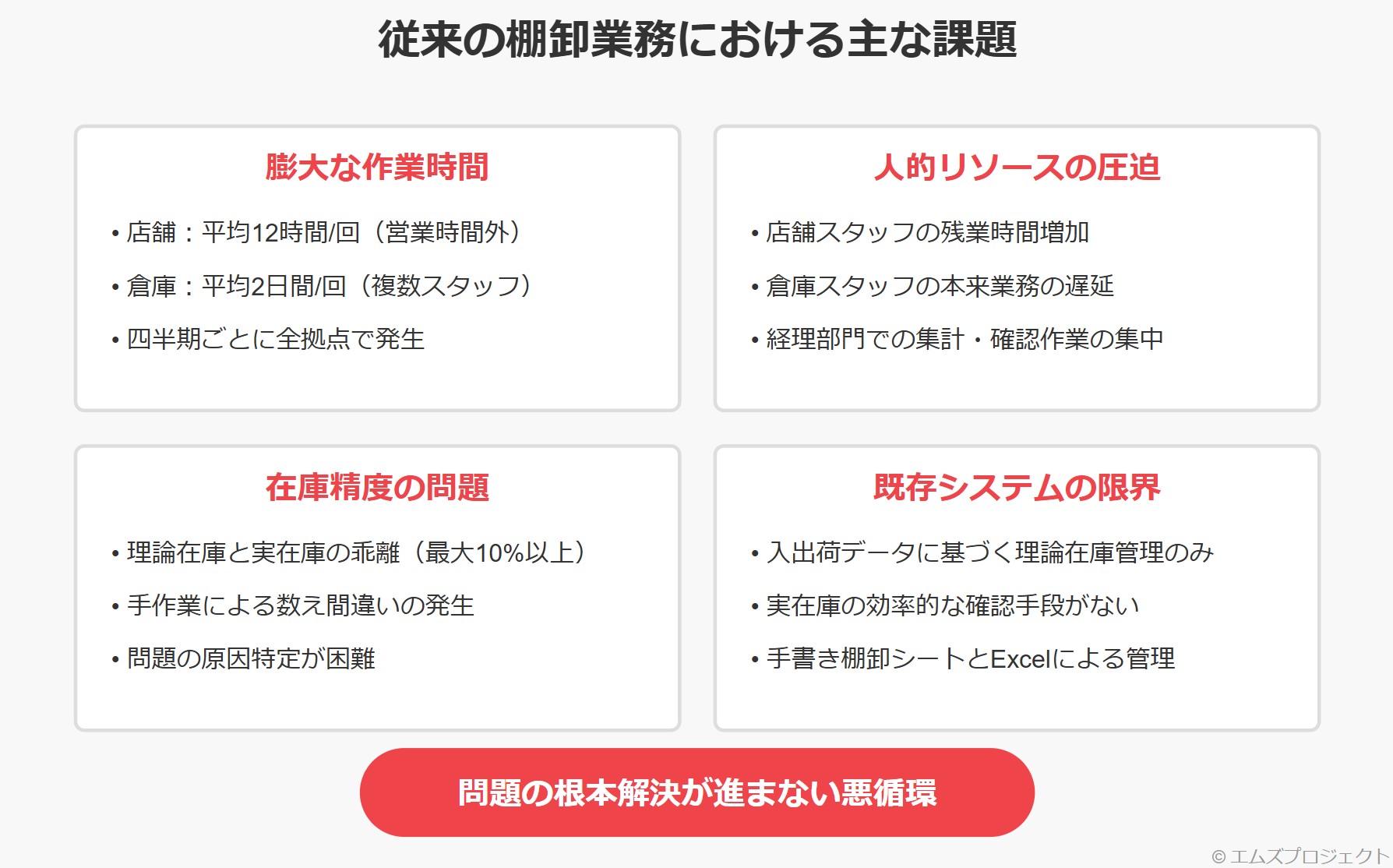